Know How to Maximizing Warehouse Performance with KPIs
- January 23, 2024
- Posted by: admin
- Category: Newsletter
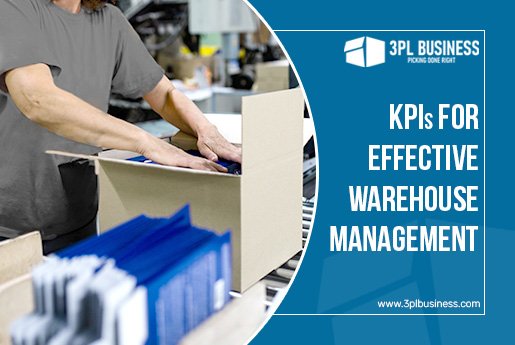
Warehousing plays a pivotal role in the supply chain process, encompassing the management of goods inflow and outflow within an organization and outside when shipping. Organized warehousing is a critical component of supply chain management, ensuring the seamless movement of in-process products from storage to manufacturing units and finished ones packaged and shipped to end consumers. As a manufacturer, whether you have your warehouse or partner with a third party logistics fulfillment provider, understanding and implementing some warehouse key performance indicators (KPIs) is essential for effective and speedy supply chain process. KPIs provide valuable insights into the efficiency and effectiveness of your warehouse processes, helping you make informed decisions to optimize operations and enhance customer satisfaction. While many warehouse management KPIs can be universally applied, tailoring them to your specific business goals is crucial. In this post, we’ll explore commonly used warehouse KPIs and their relevance, helping you identify the ones best suited to meet your objectives.
If you are looking for a warehouse management service partner or facing any challenges, you can rely on 3PL Business as your partner. 3PL Business, as an experienced player in warehouse management services, has the capabilities to address any challenges our clients have. We offer support at every fulfillment phase as a full-service eCommerce fulfillment company. Feel free to contact us today.
KPIs for Various Segments of Warehouse Management
A good-quality, high-speed software is essential for any warehouse today to track, control, and arrange goods. Another aspect is partnering with ecommerce fulfillment warehouse companies as they are experts in this segment. Aside from these two important factors, here are some KPIs for effective warehouse management considering various aspects such as inventory, safety, order management, and more.
Inventory KPIs
- Inventory Accuracy: Keeping an accurate count of your inventory is paramount. Inventory accuracy measures the alignment between tracked and physically present stock, allowing you to identify discrepancies that might arise from theft, damage, or other factors. Implement cutting-edge inventory management systems to ensure accuracy in terms of storage pattern, removal, and placement of goods.
- Shrinkage: Shrinkage refers to inventory that is recorded but no longer physically available due to theft, damage, or miscalculations. This KPI helps you understand the financial impact of losses within your warehouse.
- Carrying Cost of Inventory: Managing inventory efficiently is crucial for your bottom line. The carrying cost of merchandise measures the expenses associated with owning, storing, and holding stock. Lowering this cost frees up resources for other critical aspects of your business.
- Inventory Turnover: This KPI measures how quickly your inventory is being sold. A higher turnover indicates strong sales, while a lower turnover suggests slower sales. Streamlining of processes can help increase inventory turnover and reduce holding costs.
- Inventory to Sales Ratio: This ratio reveals the balance between the remaining inventory at month-end and the sales made during the same period. It aids in identifying cash flow issues and helps plan future stock purchases to prevent backorders.
Receiving KPIs
- Receiving Efficiency: Tracking employees’ productivity in the receiving area is vital. This KPI helps you assess the effectiveness of your receiving processes and determine whether improvements or training sessions in warehouse management are necessary.
- Cost of Receiving per Line: This KPI calculates the expenses incurred in receiving a line of products from vendors, including handling and accounting costs. It should decrease over time, indicating increased efficiency.
- Receiving Cycle Time: Measuring the average time processing for received stocks helps you identify bottlenecks and optimize receiving processes for fast inventory placement.
Putaway KPIs
- Accuracy Rate: A high accuracy rate means items are put away correctly the first time, reducing errors and enhancing warehouse efficiency.
- Putaway Cost per Line: Calculating the cost of putting away a line of items helps identify areas for cost reduction within your putaway processes. This may also include removing scrap as well as excess and redundant parts or goods.
- Putaway Cycle Time: Reducing the time to put away a single item enhances warehouse efficiency. Repositioning things can help achieve this.
Order Management KPIs
- Picking Accuracy: This KPI measures the accuracy of items picked for customer orders, ensuring orders are fulfilled correctly and efficiently.
- Total Order Cycle Time: The average time from order placement to shipment, including all intermediate processes, impacts customer satisfaction. Shortening this time improves the chances of retaining customers.
- Order Lead Time: The average time it takes for an order to reach a customer after placement, including shipping time, affects customer expectations. Faster order lead times enhance customer satisfaction.
- Backorder Rate: A high backorder rate indicates the need for better forecasting and inventory tracking to prevent customer dissatisfaction.
- Fulfillment Accuracy Rate: Calculating the percentage of orders successfully fulfilled, from start to finish, helps identify areas for process improvement.
- On-Time Shipping Rate: Maintaining a high on-time shipping rate is crucial to prevent customer dissatisfaction.
- Cost per Order: This KPI evaluates the cost of fulfilling a customer order, helping you manage expenses and improve profitability.
- Rate of Returns: Monitoring the rate of returns assists in understanding customer satisfaction and identifying areas of improvement in your order management processes.
Safety KPIs
- Accidents per Year: Tracking notable accidents in the warehouse provides insights into safety risks and helps implement preventive measures.
- Time since Last Accident: Maintaining a high duration since the last accident demonstrates a commitment to warehouse safety.
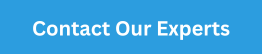
Finding the Ideal 3PL (Third-Party Logistics) partner or optimised warehouse management services and eCommerce fulfillment solutions?
Effective warehouse management involves tracking and optimizing KPIs to enhance efficiency, improve storage, reduce costs, and improve customer satisfaction. Whether you manage your warehouse or partner with a third-party logistics fulfillment company, integrating these KPIs into your operations can lead to an effective and streamlined e-commerce fulfillment process. Remember that choosing the right KPIs aligned with your business goals is critical to achieving optimal results in warehouse management. 3PL Business is an expert in this segment and a reliable player to partner with for all your pick pack and ship warehouse needs. Feel free to connect with the team for effective warehouse management. To explore how 3PL Business can streamline your warehouse management processes, contact us at (732) 983-4801 or email sales@3plbusiness.com. Our experts are ready to tailor solutions to your specific needs.